Blog
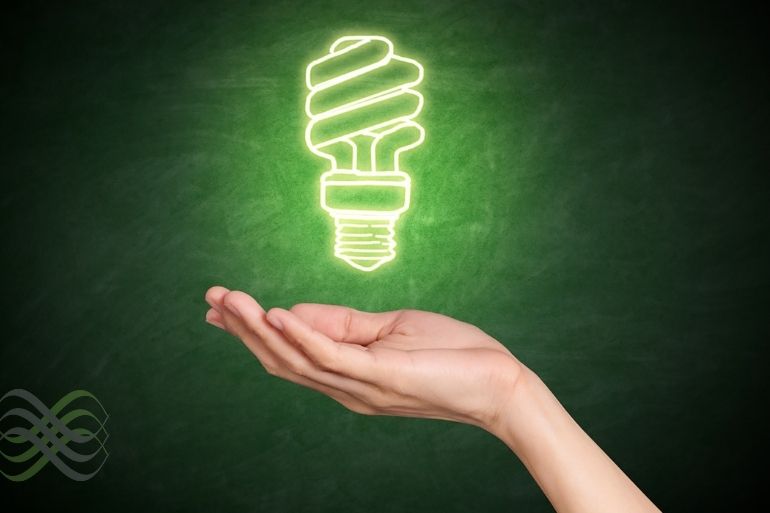
Expert Interview: Dr. Kushare On Energy Management
With such a broad scope and a huge range of opportunities for its applications, how does one define ‘Energy Management’?
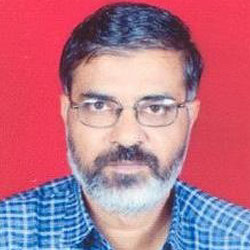
Dr. Kushare is a Phd. (Electrical) form Govt. College of
Engineering, Pune and currently the Head of Electrical
Engineering Department K.K. Wagh Institute of Engg.
Education and Research. A certified Energy Auditor of BEE
(2004 Batch), he regularly presents research at conferences,
workshops and journals dedicated to electrical field within
India and other countries. He has also authored several
technical books on the subject along with a Handbook on
Energy Efficient Motors.
Dr. Kushare advises companies on energy management and
audit, power quality audit and critical problem solving. As a
consultant he has also designed electrical installations of
several industrial and commercial establishments in India and
abroad. His expertise in energy efficient and power quality
tolerant designs and low investment driven approach to
energy management is well acclaimed.
Why do you say that ‘judicious’ and ‘effective’ aspects are ignored?
Simply because there is little evidence to believe that our design, operations and maintenance are judicious or effective in terms of energy usage. Being judicious begins right from the design stage. Firstly, loosely defined system requirements are a problem. With vagueness in requirements system remains non-optimized and ironically, programmed to waste energy.
Over dependence on thumb-rules for design is fatal to energy management
Secondly, over-dependence on thumb rules for design is fatal to energy management. Many times safety margins in design are kept at 30% to 50% more than the ideal. In fact one should aim to achieve 10% to 15% safety margins, through use of innovative techniques and latest technology.
Can you elaborate with some examples?
Sure. For example, I have observed that typically, the induction motors in the process industry have a service factor of 50% to 60%. In most cases the designer is not given adequate inputs, lowering the designer’s confidence and inflating the factor of safety. Also, users many times forcefully build an overcapacity in design with a view to accommodate any future expansion.
Today, we need to adopt an innovative modular approach in design which has the flexibility to scale up with changes in requirements.
A relatively common example in this context would be the approach taken to design Air conditioning or lighting systems. Rule of thumb based calculations do not include factors like environmental conditions (temperature, altitude, window directions etc.) which can be intelligently turned to ones advantage during design for saving energy. Being judicious is about being responsible – it’s the ability to arrive at what is enough and avoid the trap of oversizing or creating over capacities.
Further to the definition of energy management in your answer to the first question – Can you elaborate on ‘effective’ use of energy?
Effectiveness is a measure of the conversion of energy from one form to another. Procuring energy-efficient gadgets are the starting point (and not the final destination as often perceived) in energy management.
In procurement, the objective is to save costs upfront and go for cheaper options while overlooking the ‘use costs’. For example, an industrial motor with 84% efficiency running for 3,000 hrs pa with a life of 15 years has operating costs of about Rs. 85 Lacs and initial costs of over-dependence on thumb-rules for design are fatal to energy management just Rs. 1 to 1.5 Lacs. Being energy effective is about achieving the break-even between technical performance and commercial capabilities. Also, the focus needs to shift from initial costs to lifecycle costs.
What do we need to consider while assessing ‘life cycle costs’?
Life cycle cost has two major components, energy costs and maintenance costs. While energy costs are largely a determinant of equipment efficiency, maintenance costs play a key role in sustaining these efficiency levels.
Often it’s the small changes that bring the big impact. Take, for example, auxiliary equipment like cooling fans. These, typically, have a Windage loss of about 2% of rated capacity. Now, if you can minimize this loss overall such fans, the overall savings could be significant. This loss is related to the weight and speed of the fan. The fan that is of metal die-casted type has more weight and hence greater loss. But an FRP fan with its smooth profile and lightweight will be more efficient. Energy management in such cases is nothing but applied commonsense.
What according to you are the challenges for implementation of energy management initiatives?
First, most often, people overlook the importance of teamwork in energy management. For example, during the design stage, stakeholders of a typical project like project managers, architects, consultants – electrical, HVAC etc. have very little or no discussion focused on energy management. Focus is only on driving the completion of the project in a given time and financial budget. A good design is the foundation of energy management and is decisive in terms of the leverage one can achieve from it once the operations begin.
Over dependence on thumb-rules for design is fatal to energy management
Secondly, energy management is thought of as a project with a start date and end date. Implementation should be viewed as a continuous, iterative process that demands a high level of professional willpower to bring about effective and efficient use of energy. For many of our clients, significant savings in power came during the second or third cycle of implementation.
Third, commitment to energy management from every person in the organization is critical. While a lot of effort goes into budgeting, designing, strategizing energy management, sensitizing the operator which according to me is the most important factor in implementation is often left to chance. Regular training, sensitization, constant encouragement and involvement of operators in maintenance are vital to energy management.
Also, operations/ production activity should be aided with smart modifications especially in areas where it is relatively difficult to change the behaviour. For example, for one of our clients, we have a PLC that cuts the power supply during lunch break or shift change. In another case, for a large cable manufacturer, we observed, that extruders at the shop floor required simultaneous blower operation. However, the switches for both equipment were separate and operators many times left the blower on. A simple motor interlock now puts both the extruder and blower on and off at the same time, saving energy and costs for the company.
You have been consulting companies on energy audit and management over the last two decades now. How do you see the change in awareness, penetration and successful implementation of energy management in various industries?
Well, the awareness about the need for energy management is increasing. However, what bothers me is the low awareness of possibilities of better energy management in terms of approach, the magnitude of savings etc. In India, we still do not have strong industry-wide benchmarking with respect to specific energy consumption.
In India, we still do not have strong industry-wide benchmarking with respect to specific energy consumption
In terms of penetration, the approach towards energy management by many companies is still award driven/ centric. The smaller and mid-sized companies are still at bay in terms of energy management. Given their number, these companies can make a huge impact. Energy management reports are still difficult to implement. The consultants conducting energy audits needs to make the practical adaptability of their recommendations the highest priority.
From a customer perspective, the shift from ‘saving’ driven fees as opposed to the current system of ‘audit project’ based fees to consultants can bring about this change. I feel if the small and mid-sized companies are to take up the cause of conserving energy through energy management, we need to aggressively promote a cost or low investment approach to energy management.
However, it is unfortunate to still see many companies missing out on the most basic opportunities in energy management. For example, companies need to thoroughly study their electricity bill. In India, we still do not have strong industry-wide benchmarking with respect to specific energy consumption
How are you charged for energy? – in many states we have the time of the day type tariff for industry, one can take huge advantage of power factor or load factor incentives. Companies should put in more effort to have a clear idea of what they can do themselves and where you need to call experts.
What specific advice would you give to companies about ‘do it yourself’ energy management?
Learn and innovate to turn disadvantages to your advantage. We have penalties for power factor slip-ups. Now I have observed that many experienced professionals have this notion that you need to maintain a power factor rating that averages out to unity at the end of the billing cycle, when in fact, any deviation in power factor is penalized. One needs to maintain a power factor of real-time unity. Other areas of focus could be reactive power management, parametric optimization and fine-tuning of processes.
What is the focus of energy management as a discipline in near future?
Energy re-use or recycle is the biggest focus area
Energy re-use or recycle is the biggest focus area. Rising energy costs, technology improvements that allow harnessing tiny opportunities in energy and enterprises committing themselves to the cause of conserving energy are some of the drivers for these focus areas.
Sir, thanks a lot for your time and inputs. We are sure these inputs are of great help to our readers. Thank you